As you guys can tell, I don't come here much. But this is for Super Noober.
Before i start, everything can be found here. And yes, all i had was an 220 AC arc welder lol
It is designed to peak at 8500RPM, port timing is 185 exhaust 118 transfers, with triples welded intake with extra large boyesens. Reeds have been upgraded to a blaster reed cage with power reeds. blaster carb(i have a 28-29mm round slide for it). Nicer than blaster carb at least.
It's flywheel is maybe 6 ounces less than the blaster, no counter balance shaft, auto clutch modded to stall out until maybe 3-4k RPM. Pod filter. Plenty of torque, Power band is very wide. The ass dyno says it pulls from 5k-8-9k? maybe more lol who knows.. I need a tach.
The pipe is designed to match the port job, and carb size is designed to match the flow rate at my target RPM.
At the dunes, with stock pipe, I passed Nathans blaster going up the dunes lol. Always fun to up-shift flying up dunes
That thing weighs to much for that engine though. 220lb on a 175cc engine? it needs to go on a diet.. I just don't know what can be removed lol
Oh yeah, the 3 wheeled side of the port job. http://www.3wheelerworld.com/showthread.php?127930-VIDEO!!-Drilling-triple-ports-in-a-cylinder-another-video-on-page-3/page3
Before i start, everything can be found here. And yes, all i had was an 220 AC arc welder lol
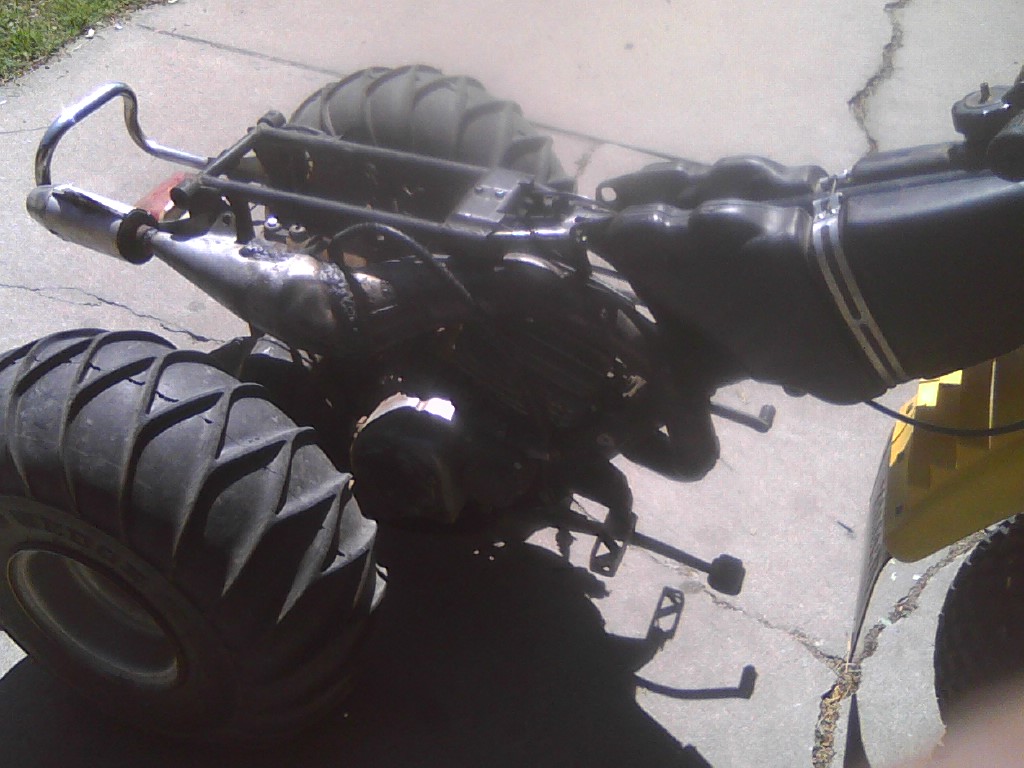
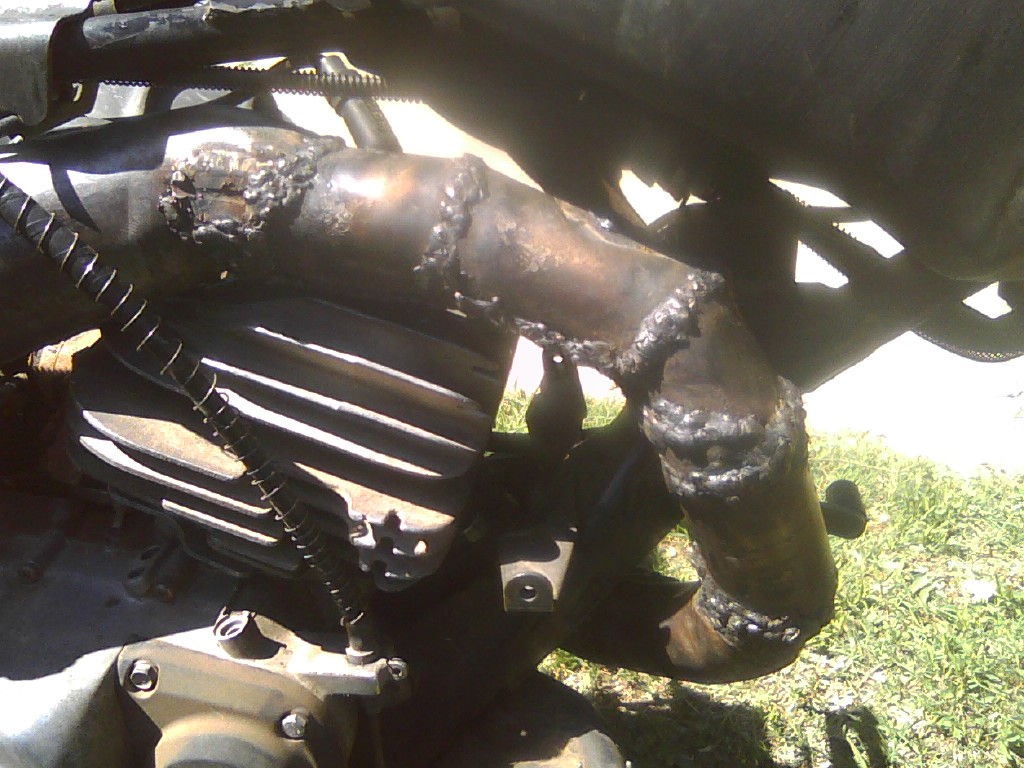
It is designed to peak at 8500RPM, port timing is 185 exhaust 118 transfers, with triples welded intake with extra large boyesens. Reeds have been upgraded to a blaster reed cage with power reeds. blaster carb(i have a 28-29mm round slide for it). Nicer than blaster carb at least.
It's flywheel is maybe 6 ounces less than the blaster, no counter balance shaft, auto clutch modded to stall out until maybe 3-4k RPM. Pod filter. Plenty of torque, Power band is very wide. The ass dyno says it pulls from 5k-8-9k? maybe more lol who knows.. I need a tach.
The pipe is designed to match the port job, and carb size is designed to match the flow rate at my target RPM.
At the dunes, with stock pipe, I passed Nathans blaster going up the dunes lol. Always fun to up-shift flying up dunes

That thing weighs to much for that engine though. 220lb on a 175cc engine? it needs to go on a diet.. I just don't know what can be removed lol
Oh yeah, the 3 wheeled side of the port job. http://www.3wheelerworld.com/showthread.php?127930-VIDEO!!-Drilling-triple-ports-in-a-cylinder-another-video-on-page-3/page3
Last edited: