The 1" material from mcmaster-carr is $37 for 6'. That's $6.16 a foot. I bought it for $5.66 a foot and found it a little cheaper elsewhere but in a limited selection.
I worked on the shock mount tonight. I have the location hammered down for the making the rest of the jig but I'm not particularly happy with the right side lower control arm shock mount. I may actually purchase more 1" tubing sometime after I have rode this set of arms and rebuild the right lower control arm using the jig to make it pretty and to the dimensions I really want.
I also measured the suspension throw. 8 3/4" without bind
Pics for you people:
I worked on the shock mount tonight. I have the location hammered down for the making the rest of the jig but I'm not particularly happy with the right side lower control arm shock mount. I may actually purchase more 1" tubing sometime after I have rode this set of arms and rebuild the right lower control arm using the jig to make it pretty and to the dimensions I really want.
I also measured the suspension throw. 8 3/4" without bind
Pics for you people:
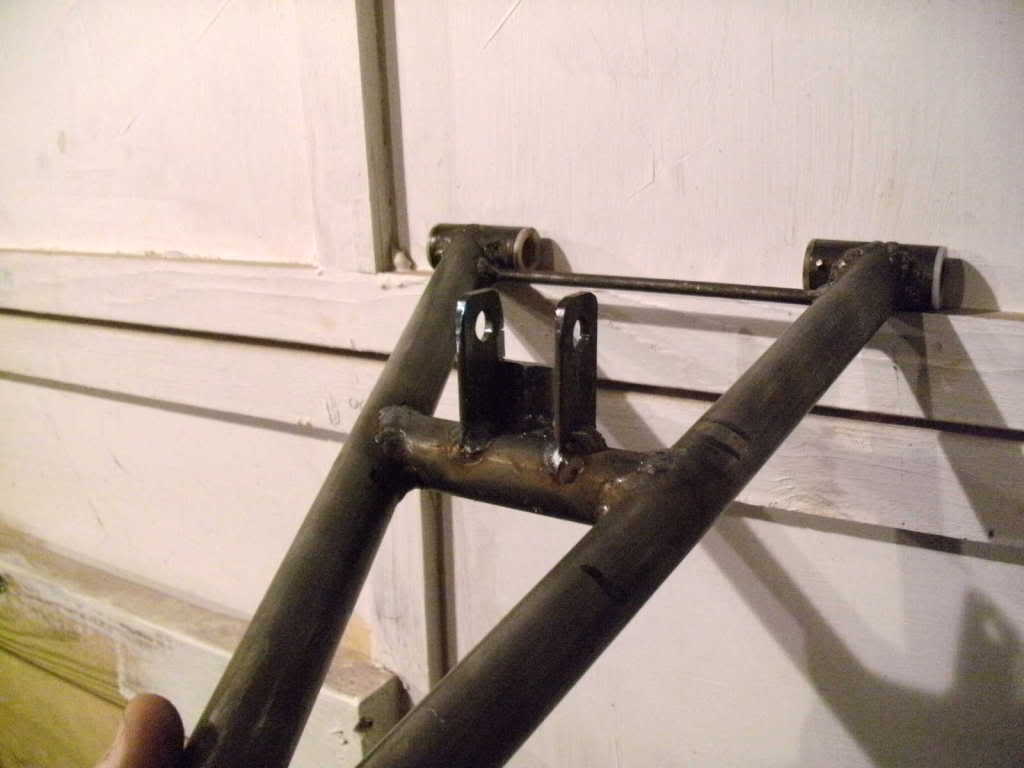
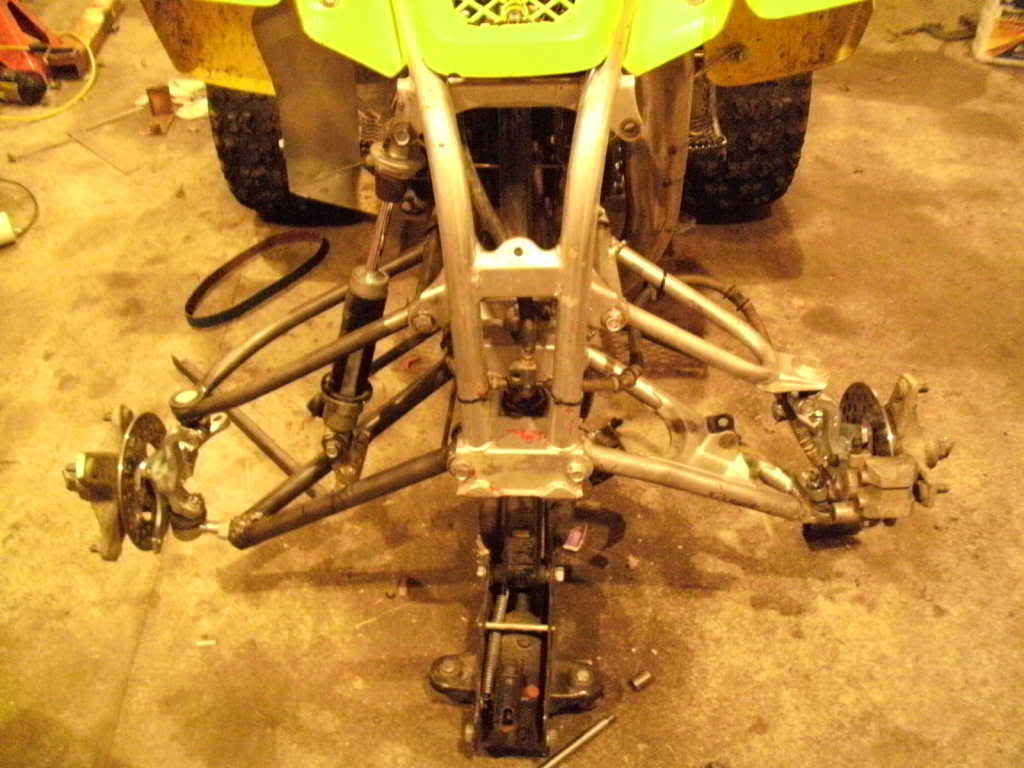
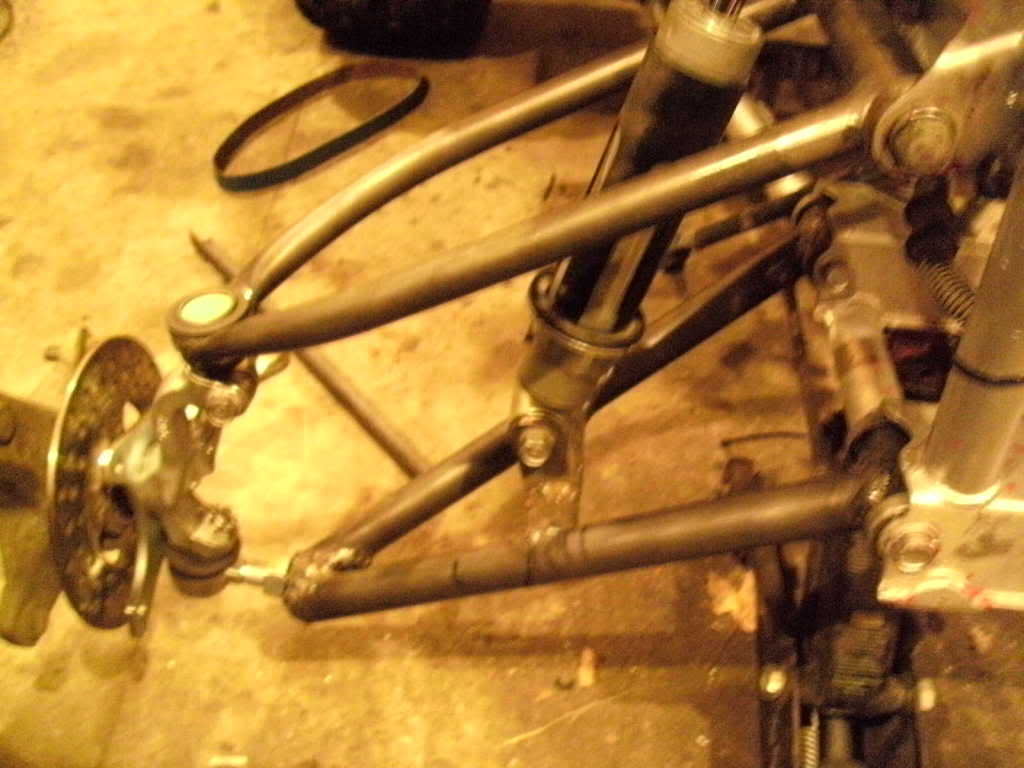
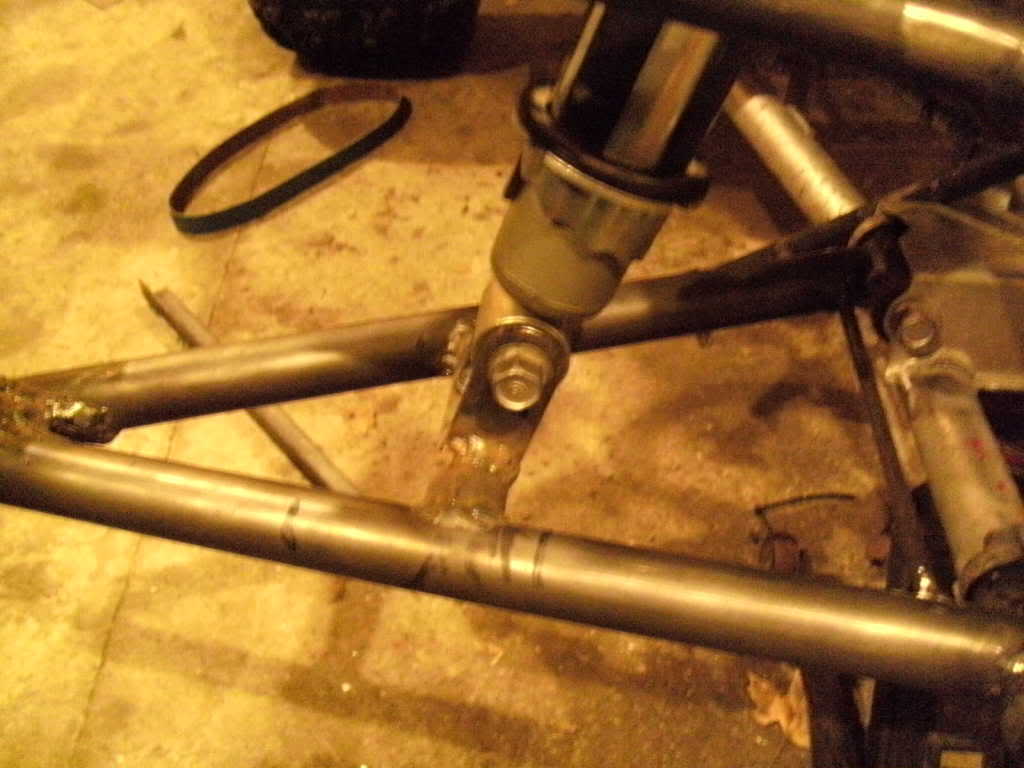
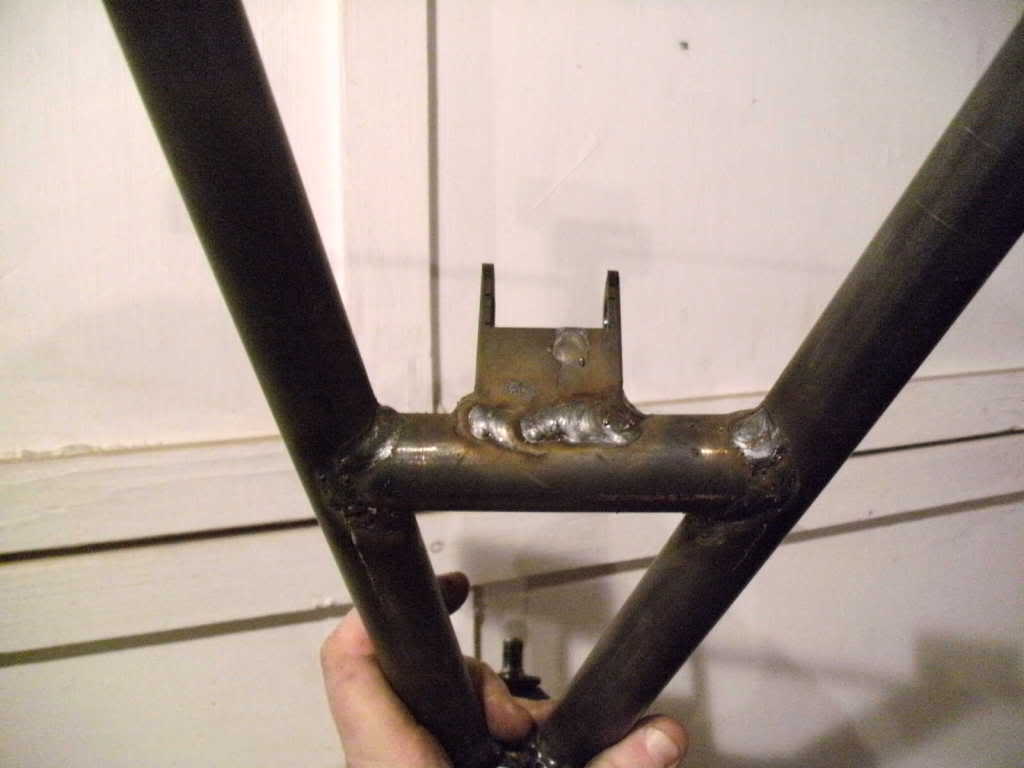