Since all this great info has been floating around on the forum about doing your own head mod I decided to give it a try. First I made my arbor made from stainless scrap I had. Pretty nice if I dont say....
Cutting the Head: Toroidal Based
Im posting this for other members who know more about this than I do, to please correct me or guide me in making this better.
First I cleaned up the gasket sealing surface and brought it down flush with the casting. The head had some run out in it thats why in the pics the cut isn't perfectly centered around the spark plug but its all flush where the sealing gasket makes contact and thats what matters. Then I dived in to make a 68mm ring 8 thousands deep. The 8 thousands came from: (.040"-.032" head gasket thickness)... Not sure what the purpose was but thats how I was told to do it. :-/ Then I set my compound rest to 11 degrees and cut the squish band back to that 8 thousand deep ring. Then I was told to cut the combustion chamber a diameter thats 55% of the bore size at relatively the same angle as the stock combustion chamber angle. I have a bore size of 60 over or 67.5mm and from playing around I found that the stock combustion chamber appeared to be at 60 degrees. So I then set my compound rest to 60 degrees and started cutting away until I reached 37mm (67.5mm x 55%) in diameter. Then I sanded the head and polished lightly with a fine scotch bright pad.
Now like I said Im sure I have mistakes in this but Im learning. I wanted to give it a try and see where this gets me. Now I know your suppose to cc the head but I havent had a chance to do that yet. Since both my blasters are in rebuilds currently Im giving this head to 92f150300six to try out and give me an ass dyno report compared to his stock head. And see if this is any better or worse.
So here's the pics....
My Arbor:
I used a lage diameter piece of stainless so it would be easier for my three jaw chuck to grab and center it with less run out. Has 7/8 flats milled on it to be able to use a 7/8 open end wrench.
Also stamped my name on one side and the thread size and pitch on the other.
On the lathe:
After cutting the 11 degree squish band.
After cutting the 60 degree combustion chamber out to a diameter of 37mm using the compound rest with carbide boring bar.
Finished product with a light polish.
Cutting the Head: Toroidal Based
Im posting this for other members who know more about this than I do, to please correct me or guide me in making this better.
First I cleaned up the gasket sealing surface and brought it down flush with the casting. The head had some run out in it thats why in the pics the cut isn't perfectly centered around the spark plug but its all flush where the sealing gasket makes contact and thats what matters. Then I dived in to make a 68mm ring 8 thousands deep. The 8 thousands came from: (.040"-.032" head gasket thickness)... Not sure what the purpose was but thats how I was told to do it. :-/ Then I set my compound rest to 11 degrees and cut the squish band back to that 8 thousand deep ring. Then I was told to cut the combustion chamber a diameter thats 55% of the bore size at relatively the same angle as the stock combustion chamber angle. I have a bore size of 60 over or 67.5mm and from playing around I found that the stock combustion chamber appeared to be at 60 degrees. So I then set my compound rest to 60 degrees and started cutting away until I reached 37mm (67.5mm x 55%) in diameter. Then I sanded the head and polished lightly with a fine scotch bright pad.
Now like I said Im sure I have mistakes in this but Im learning. I wanted to give it a try and see where this gets me. Now I know your suppose to cc the head but I havent had a chance to do that yet. Since both my blasters are in rebuilds currently Im giving this head to 92f150300six to try out and give me an ass dyno report compared to his stock head. And see if this is any better or worse.
So here's the pics....
My Arbor:
I used a lage diameter piece of stainless so it would be easier for my three jaw chuck to grab and center it with less run out. Has 7/8 flats milled on it to be able to use a 7/8 open end wrench.
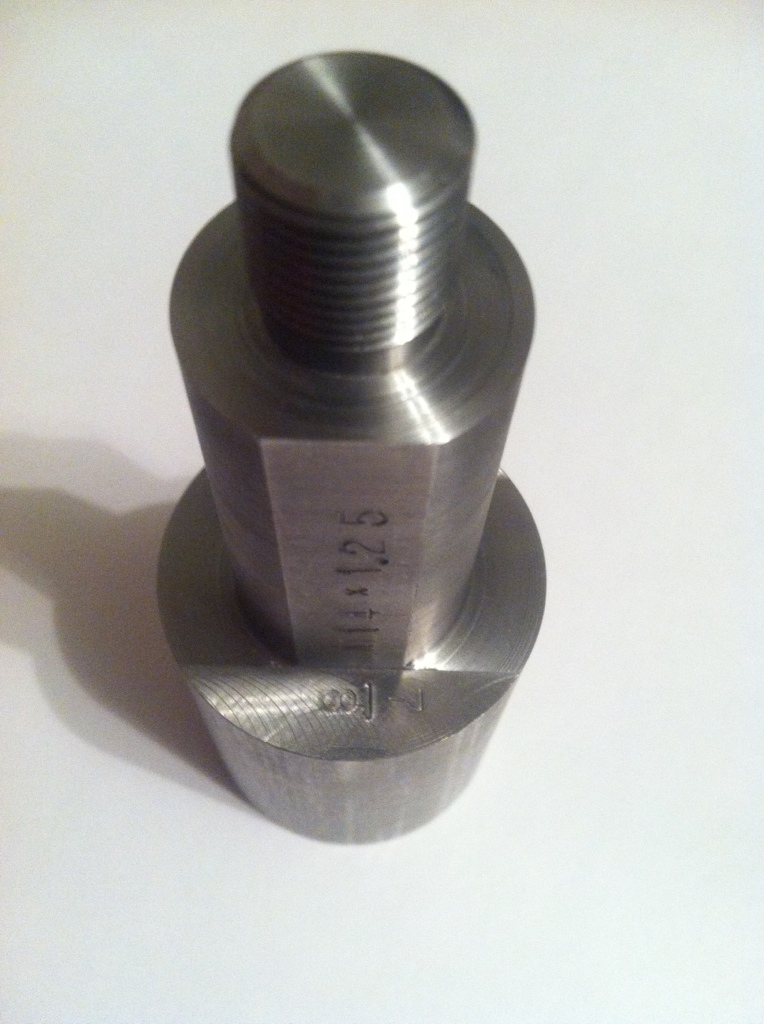
Also stamped my name on one side and the thread size and pitch on the other.
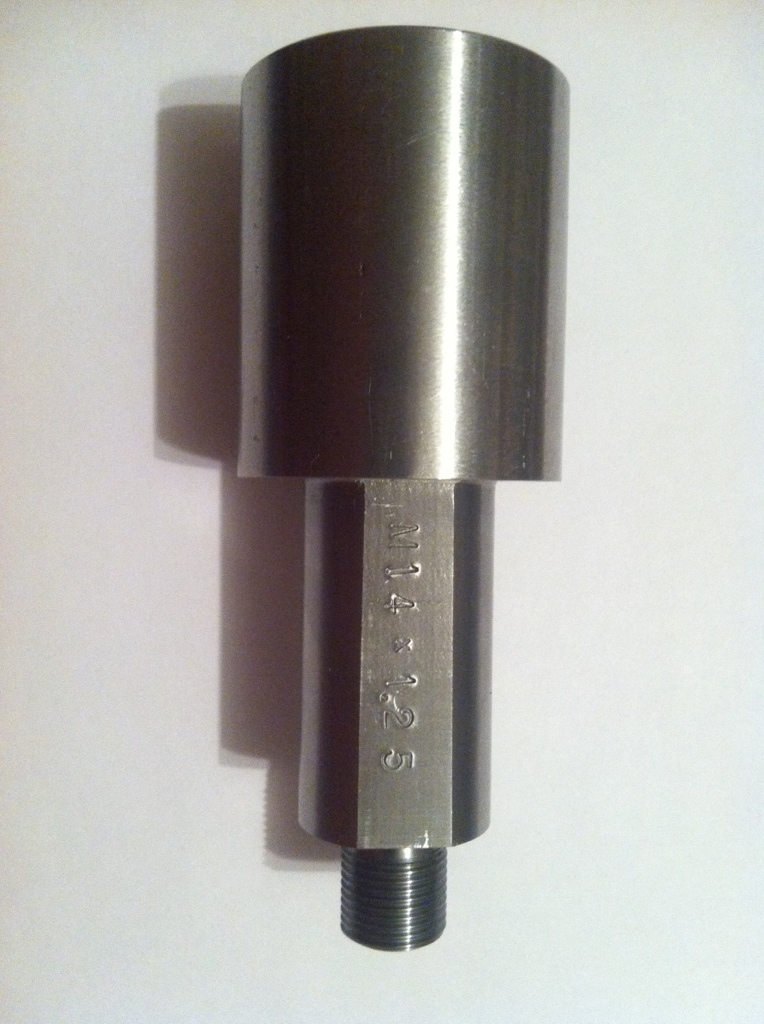
On the lathe:
After cutting the 11 degree squish band.
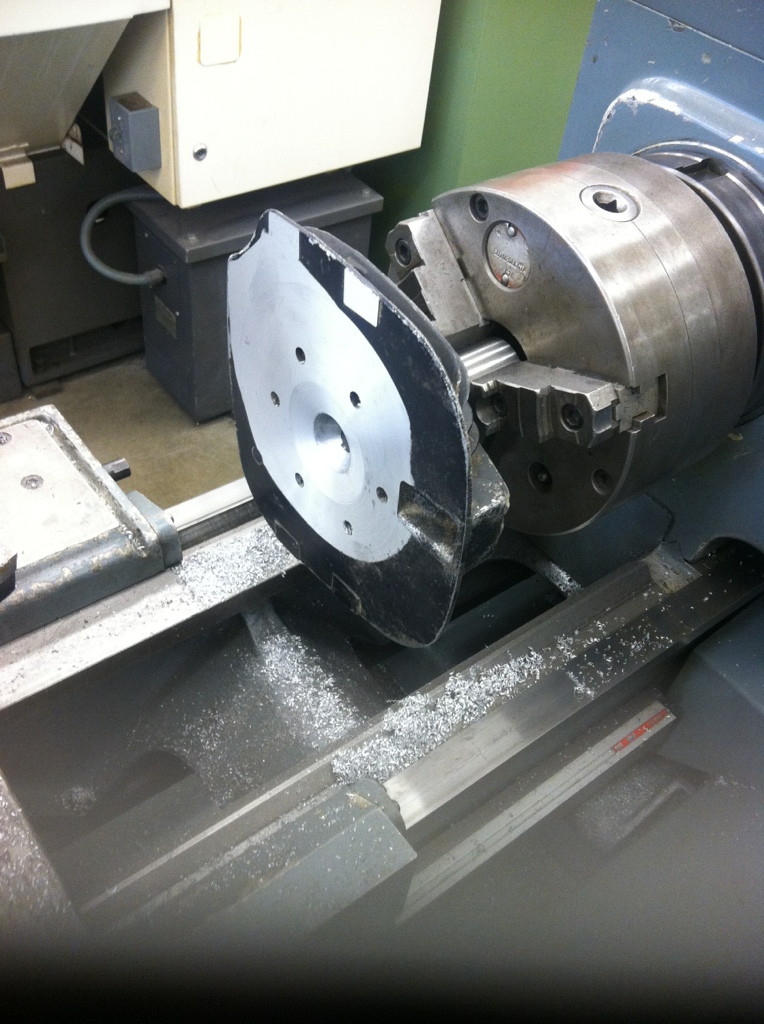
After cutting the 60 degree combustion chamber out to a diameter of 37mm using the compound rest with carbide boring bar.
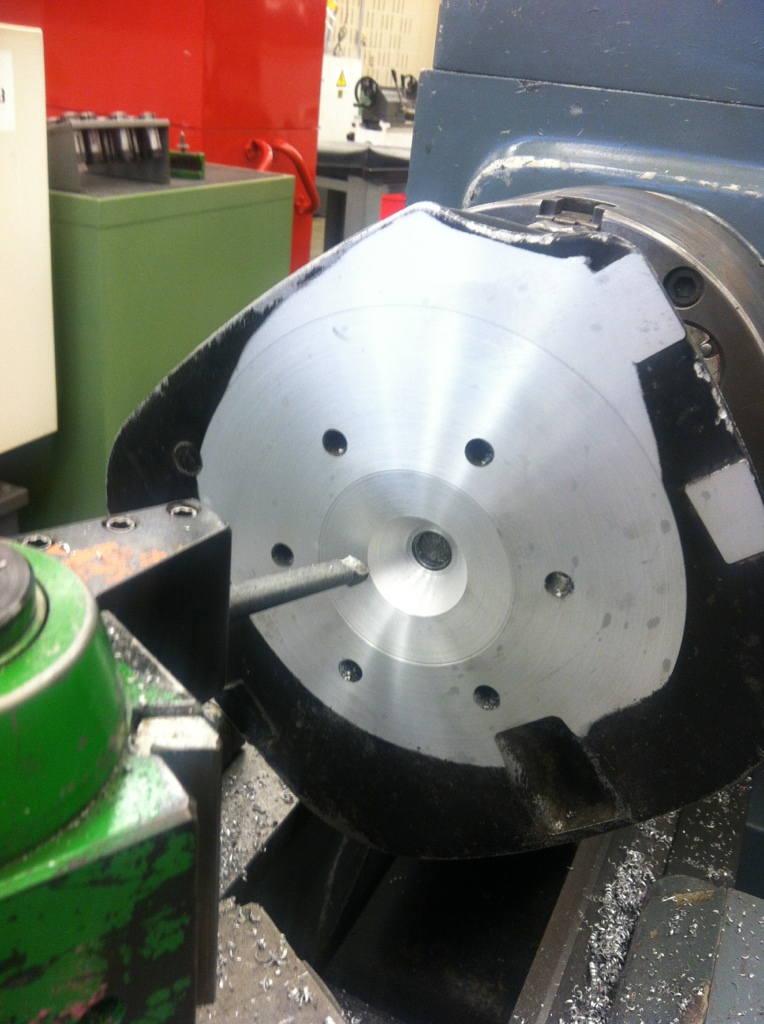
Finished product with a light polish.
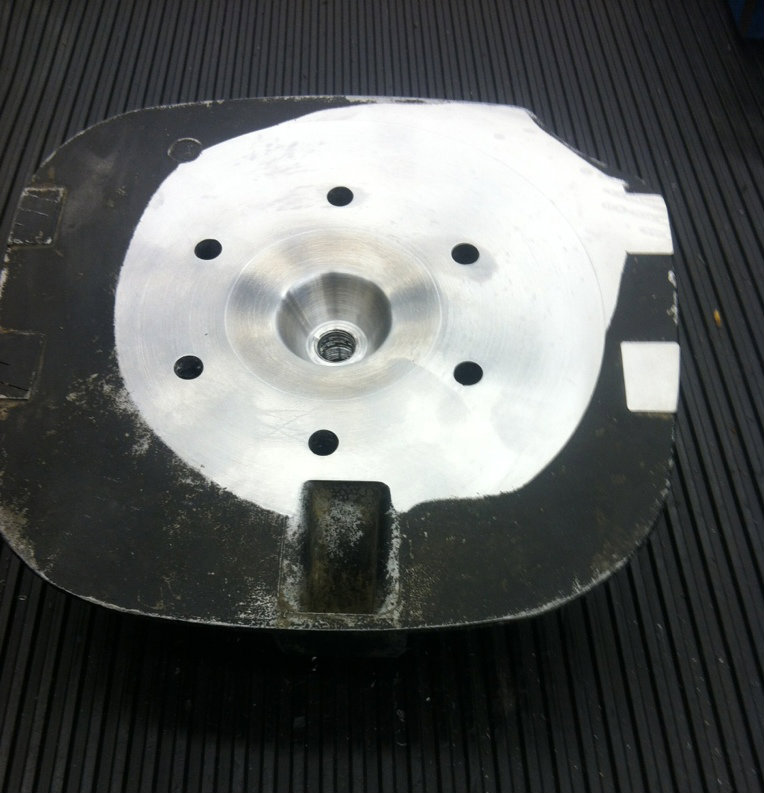