@JonS: ?????????? ok...
Here's the machine sitting in the garage, ready to go. I have it sitting on a workbench I don't like (and is really too small) and will be building a workbench from scratch to incorporate a full support, drawers, and a work bench area at the tailstock end.
Compound mounted:
VFD controls. It has a belt from the motor to the spindle but only has two steps. Spindle speeds are 50-1300 and 100-2600.
With the mast adjusted up for maximum clearance to the table.
The milling head rotates around backwards to clear out the lathe area. It turns around 360 degress.
Here's the machine sitting in the garage, ready to go. I have it sitting on a workbench I don't like (and is really too small) and will be building a workbench from scratch to incorporate a full support, drawers, and a work bench area at the tailstock end.
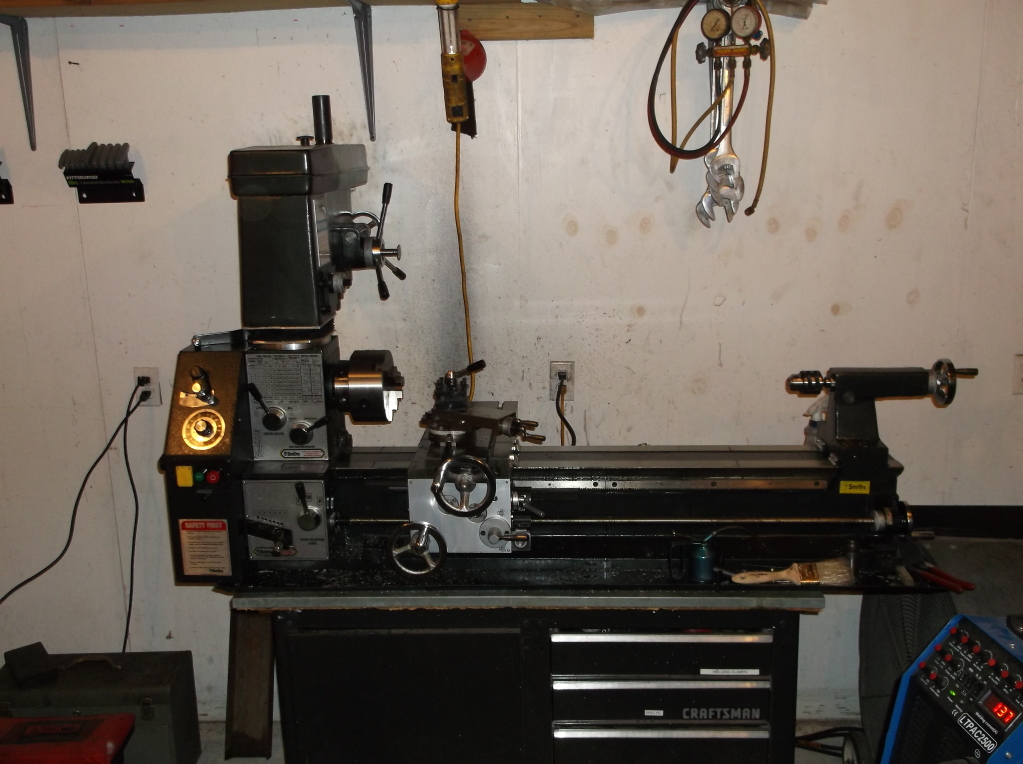
Compound mounted:
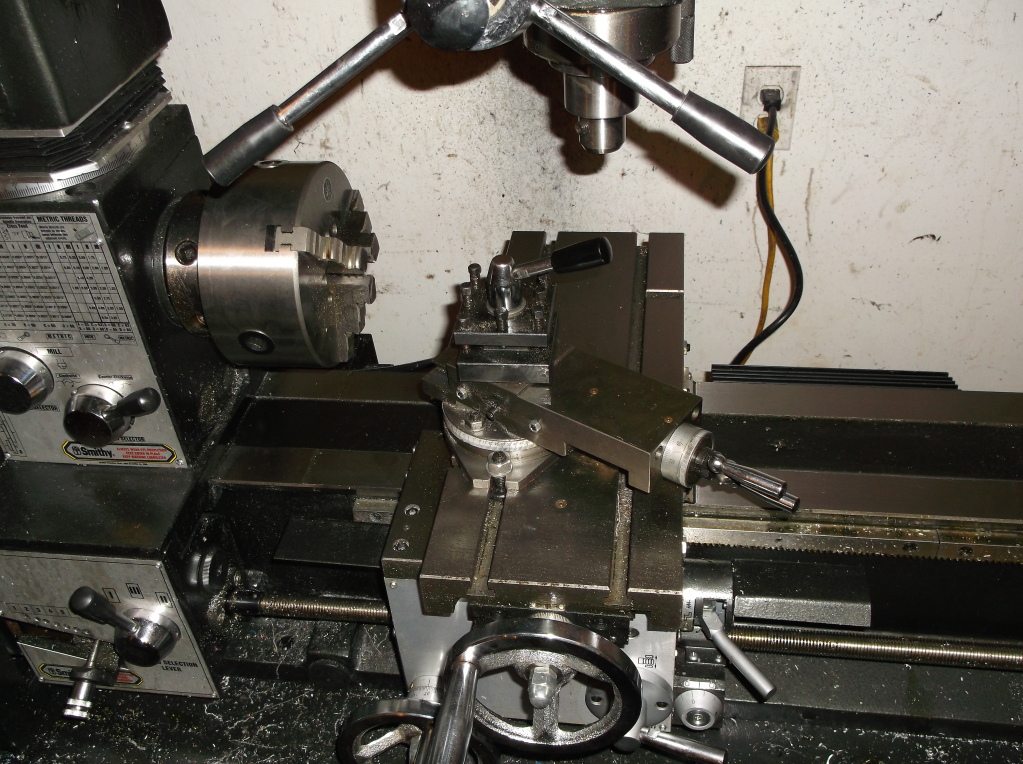
VFD controls. It has a belt from the motor to the spindle but only has two steps. Spindle speeds are 50-1300 and 100-2600.
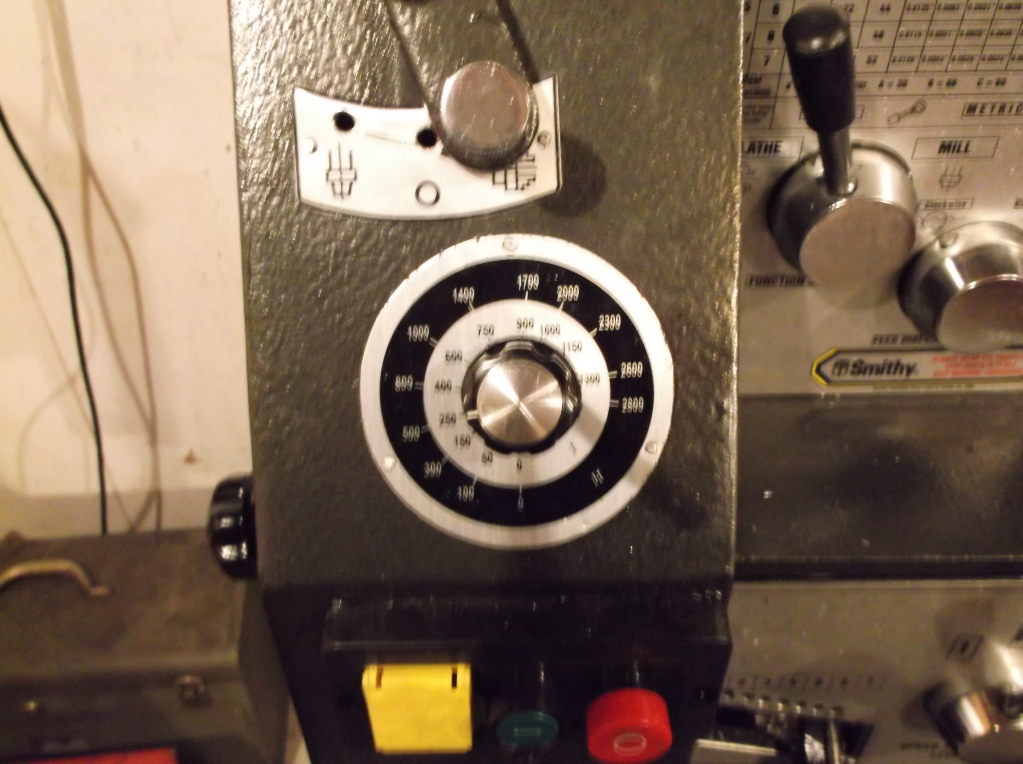
With the mast adjusted up for maximum clearance to the table.
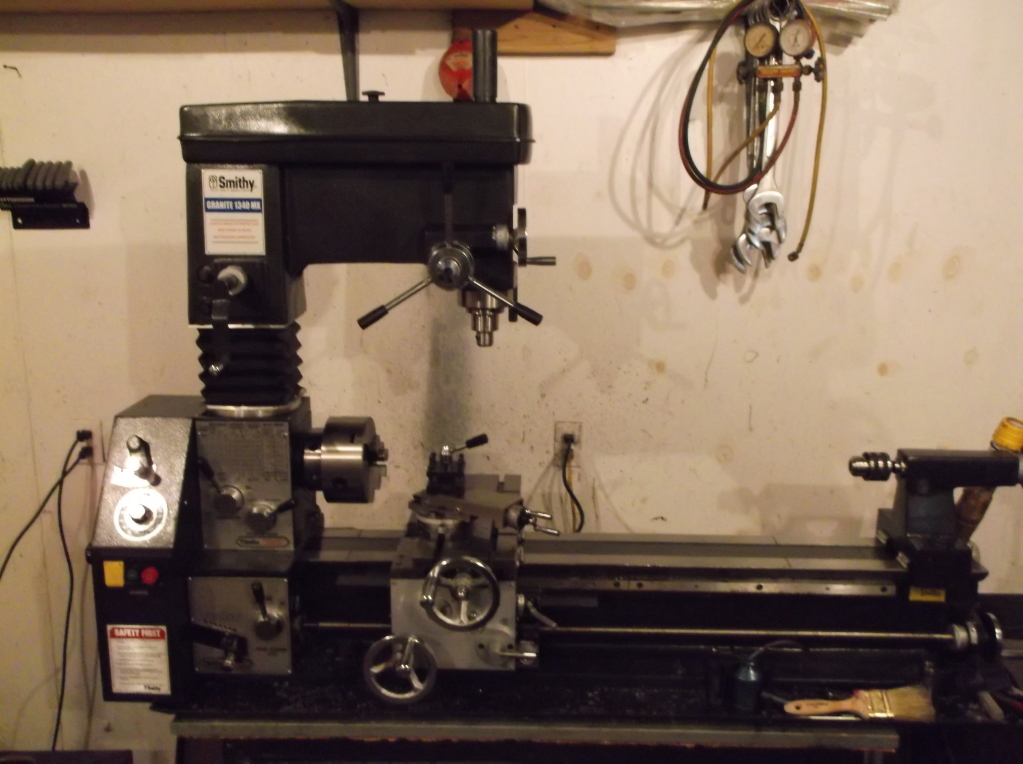
The milling head rotates around backwards to clear out the lathe area. It turns around 360 degress.