I was outside working on rebuilding a set of blaster cases (remodeling the oil drain plug area due to extensive damage) and I was using my air tools to burr away aluminum when my air compressor started making some funny noises. I went over to investigate and the pulley on the compressor end is not aligned with the motor and the belt is running funny so I unplugged it. I looked down and the set screw for that pulley had fallen out. I pulled it out of it's little hole in the corner and realized it was COVERED in oil film. I wasn't surprised, I was given the air compressor when my dad upgraded to a newer model and it needed a bunch of work when I got it... I decided to change/check the oil and put the pulley back on was in order....
I pulled the drain plug and metal shaving rolled out of the hole. I said "oh no" and went on back into the garage for the tools needed to pull it all apart. I found some damage:
Nothing insane...but bad enough to require attention. The cylinder had some pitting before but this seems much worse than the last time I messed with this compressor. I'm not sure how, but it looks like it's eating the cylinder liner from runtime....
One of the crank journals has a little mess on it. I believe that would come off with some light emery clothing and probably be fine but it feels like that rod end is worn beyond usable and will probably need replacing.
I'm kinda contemplating rebuilding this compressor head or not. Those pistons are the same diameter as 5 hp briggs pistons so I could get an oversize piston and ring set and have that cylinder side bored out. I know for a fact that the 5hp briggs rods will work in there as well because that's what's already in there (the one that's wore out now) from way back when my dad had it.
I've had this compressor for 5 years. My dad had it for 20 years prior to that. My dad got it off a co-worker who had rebuilt after buying it used at a yard sale.... I'd estimate it's age to be.....older than me!
Otherwise the compressor isn't in horrible shape. The tank is sound, the electric motor runs smooth. And before anyone even bothers... Yes, I know the switch box needs a cover.... I just haven't bothered as the air compressor has it's own corner in a little shed in the sideyard I use for storing my lawnmower...
I pulled the drain plug and metal shaving rolled out of the hole. I said "oh no" and went on back into the garage for the tools needed to pull it all apart. I found some damage:
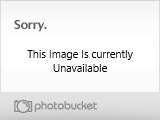
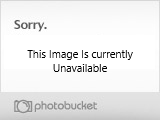
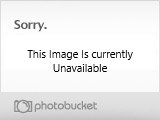
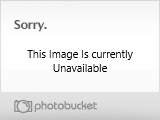
Nothing insane...but bad enough to require attention. The cylinder had some pitting before but this seems much worse than the last time I messed with this compressor. I'm not sure how, but it looks like it's eating the cylinder liner from runtime....
One of the crank journals has a little mess on it. I believe that would come off with some light emery clothing and probably be fine but it feels like that rod end is worn beyond usable and will probably need replacing.
I'm kinda contemplating rebuilding this compressor head or not. Those pistons are the same diameter as 5 hp briggs pistons so I could get an oversize piston and ring set and have that cylinder side bored out. I know for a fact that the 5hp briggs rods will work in there as well because that's what's already in there (the one that's wore out now) from way back when my dad had it.
I've had this compressor for 5 years. My dad had it for 20 years prior to that. My dad got it off a co-worker who had rebuilt after buying it used at a yard sale.... I'd estimate it's age to be.....older than me!
Otherwise the compressor isn't in horrible shape. The tank is sound, the electric motor runs smooth. And before anyone even bothers... Yes, I know the switch box needs a cover.... I just haven't bothered as the air compressor has it's own corner in a little shed in the sideyard I use for storing my lawnmower...
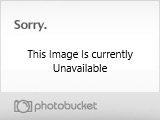
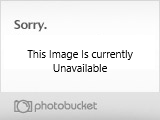