Deciding to try out somthin new. I'm sure its been done before, but I've never seen it on here. I took my DIY ported cylinder to the weld shop today, and built up some welds on the outsides near the rear of the transfer ports. My goal is to add enough aluminum on the sides to open up the boyesen ports I drilled to the maximum size possible. not exactly sure if there is any real benefit or hp gain from this mod, but its fun to experiment anywaysI:I If any of you have ever welded cast aluminum, then you know how much of a pain in the a$$ it is LOL. any ways I did a lot of pre-cleaning to avoid porosity , i used a stainless wire brush and acetone cleaner, and It welded A LOT better.
Here's some pics.
This was the first set of welds I did on the left side, didn't do enough pre-clean and it didn't "puddle up" very good leaving an ugly set of beads and alot of porosity(contamination).
Here's a better view
Here's the boyesen ports, too small and positioned too high, a thanks goes to blaaster for pointing that out to me in my other thread DIY porting.
Here's the right side, welded better but showed obvious signs of tungsten contamination(to lazy to re-prep the tungsten LOL) due to the slight black/grayish tint beside the welds, oh well haha still welded decent
Tig Welding was done with an air cooled torch, i was running at about 180 amps using AC polarity with AC balance set to max cleaning action. Anyways that SOB gets hot as hell compared to a liquid cooled torch LOL
Here's the right side after cleaning with a stainless wire brush.
That's all I have done for now, more progress and pics hopfully next week.
Here's some pics.
This was the first set of welds I did on the left side, didn't do enough pre-clean and it didn't "puddle up" very good leaving an ugly set of beads and alot of porosity(contamination).
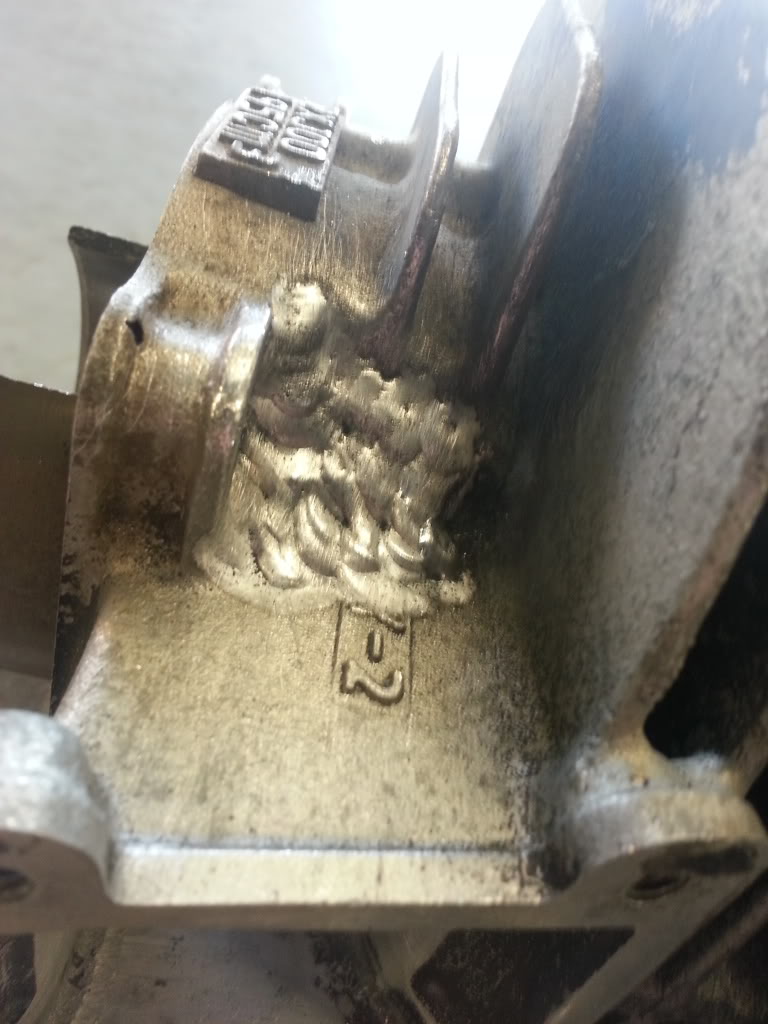
Here's a better view
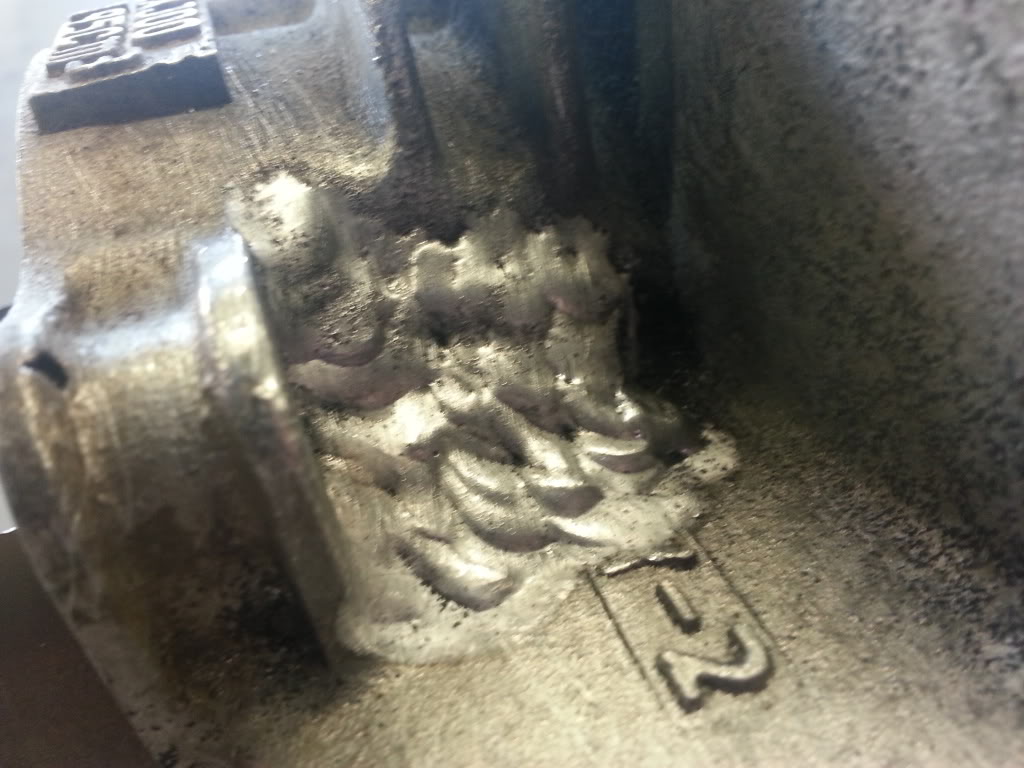
Here's the boyesen ports, too small and positioned too high, a thanks goes to blaaster for pointing that out to me in my other thread DIY porting.
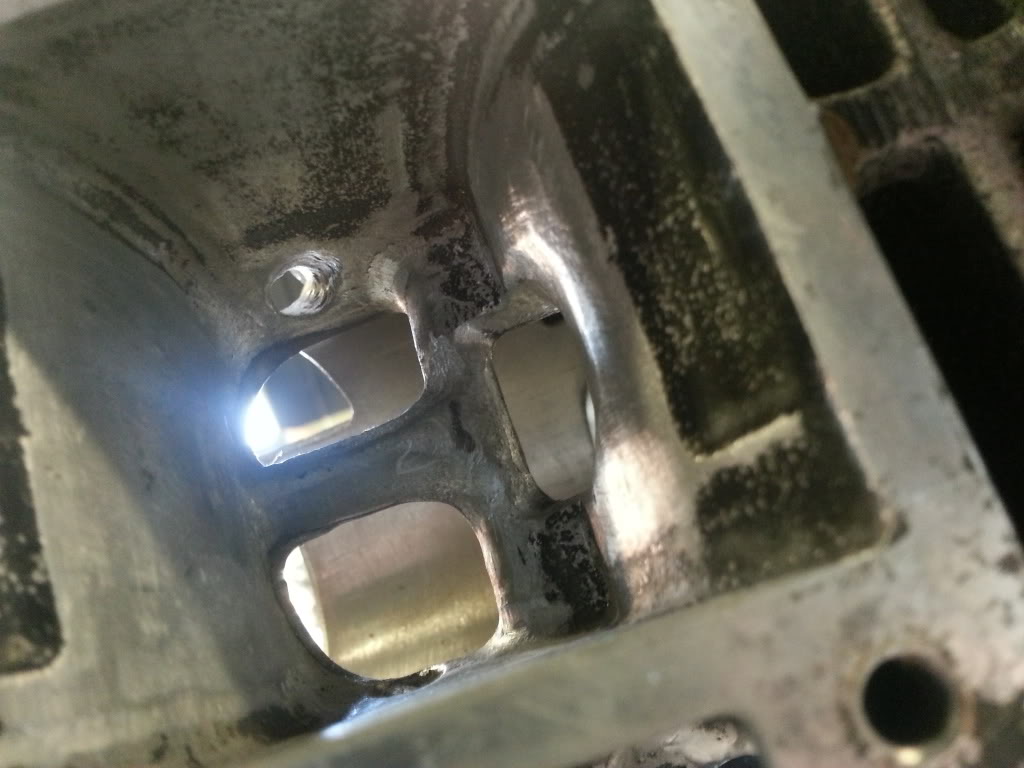
Here's the right side, welded better but showed obvious signs of tungsten contamination(to lazy to re-prep the tungsten LOL) due to the slight black/grayish tint beside the welds, oh well haha still welded decent
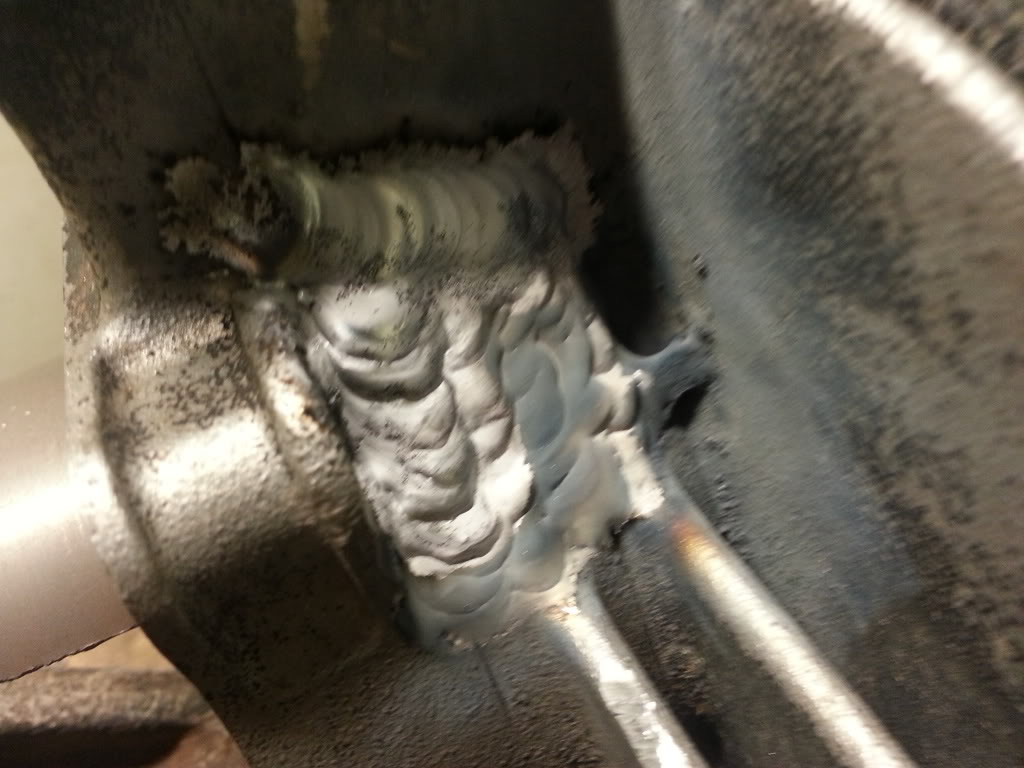
Tig Welding was done with an air cooled torch, i was running at about 180 amps using AC polarity with AC balance set to max cleaning action. Anyways that SOB gets hot as hell compared to a liquid cooled torch LOL
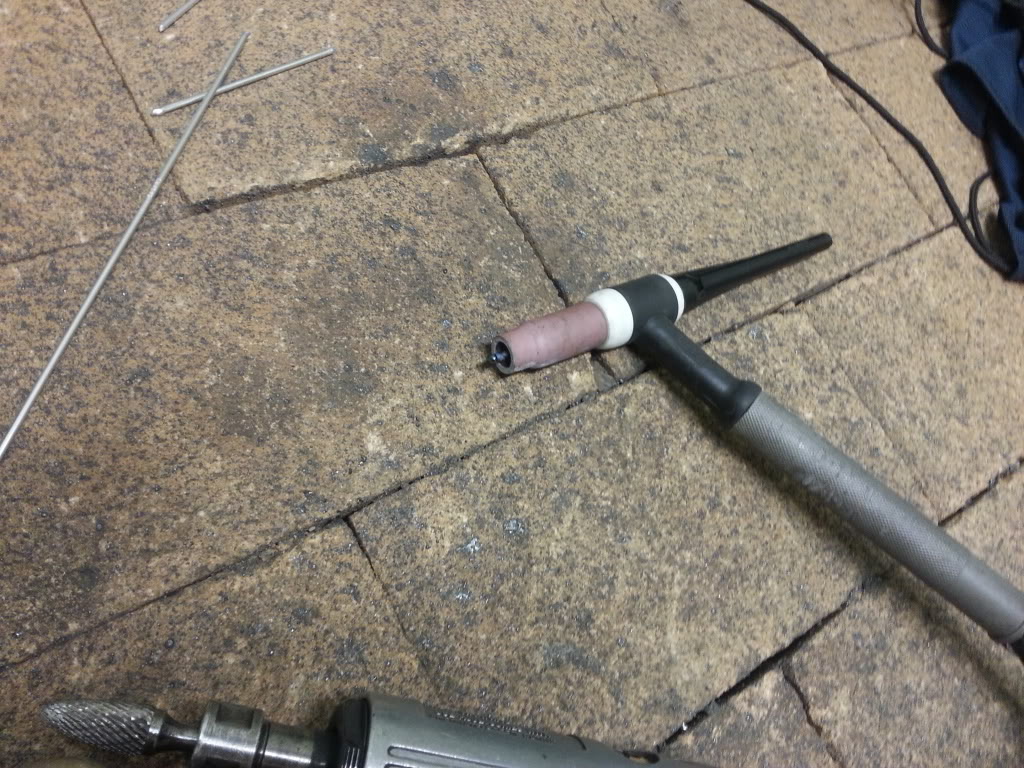
Here's the right side after cleaning with a stainless wire brush.
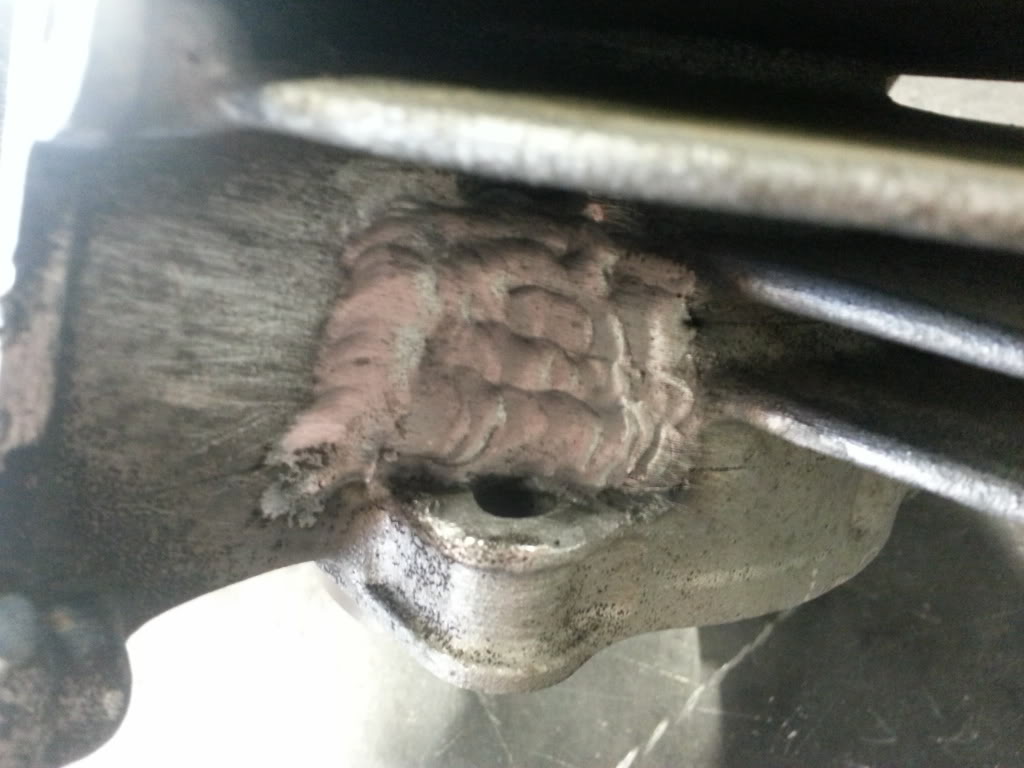
That's all I have done for now, more progress and pics hopfully next week.