Well guys, I must admit I under estimated the punishment that my bike has to endure...
A few years ago, after breaking my standard swingarm, I built my own swinger. Thinking it was rock solid, it too finally gave way...
Turns out the leverage and twisting force applied to the swingarm transmitted through the wheels is pretty enormous! Strong enough to cause metal fatique and shear right through a 50x25x2mm steel.
Its back to the drawing board!
BEFORE:
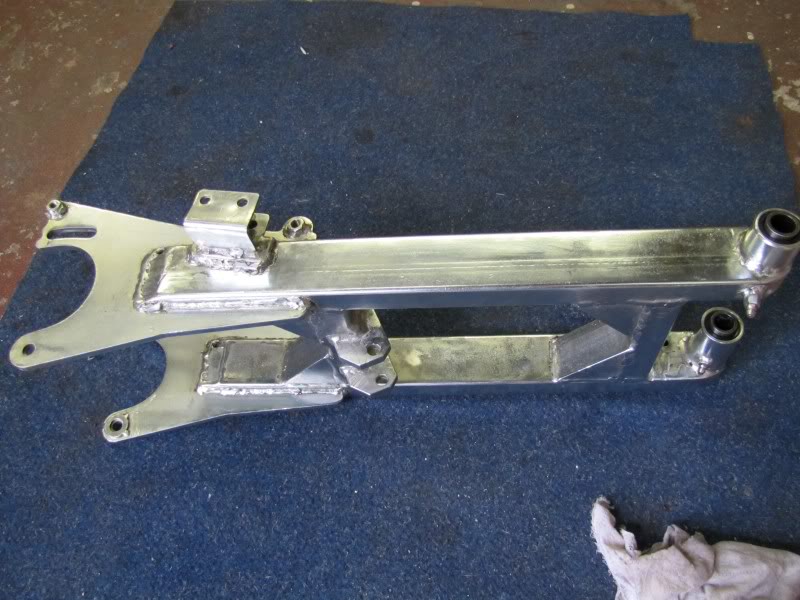
AFTER:
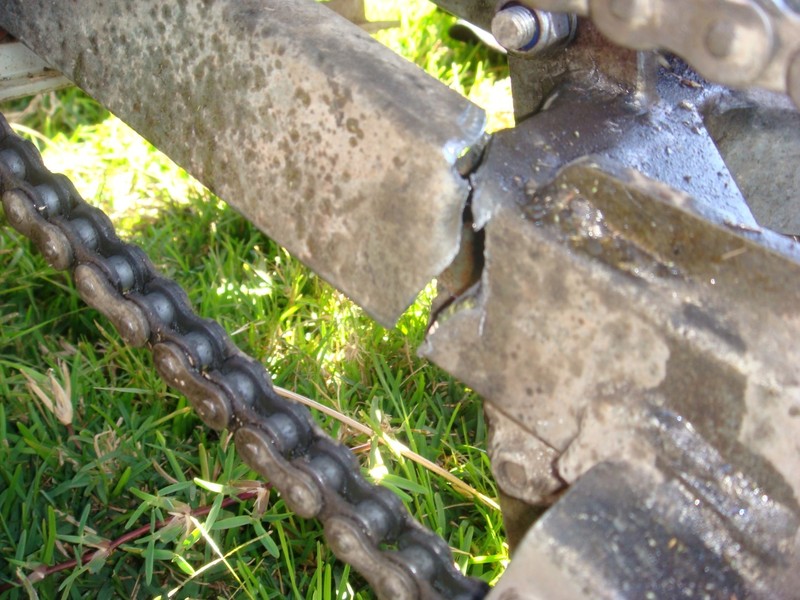
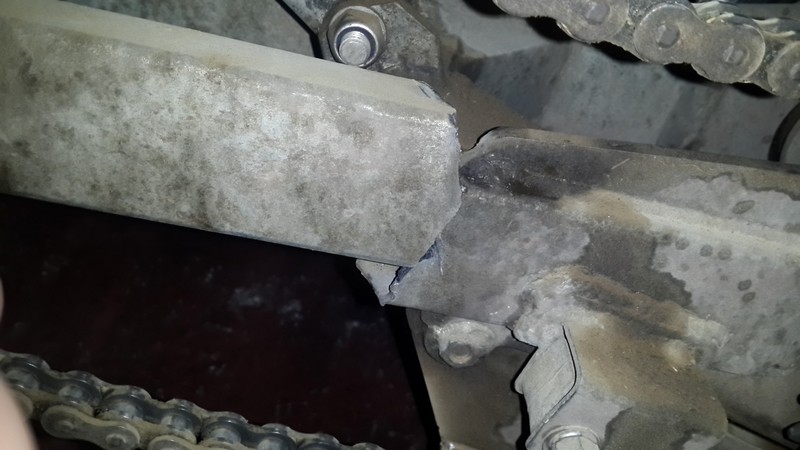
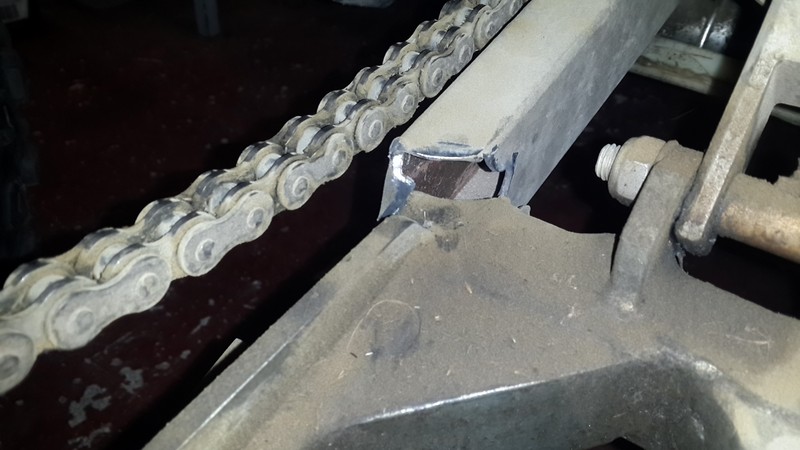
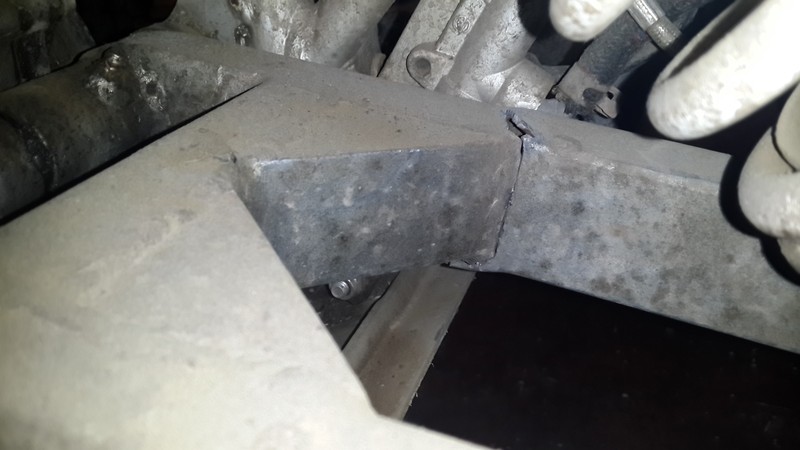
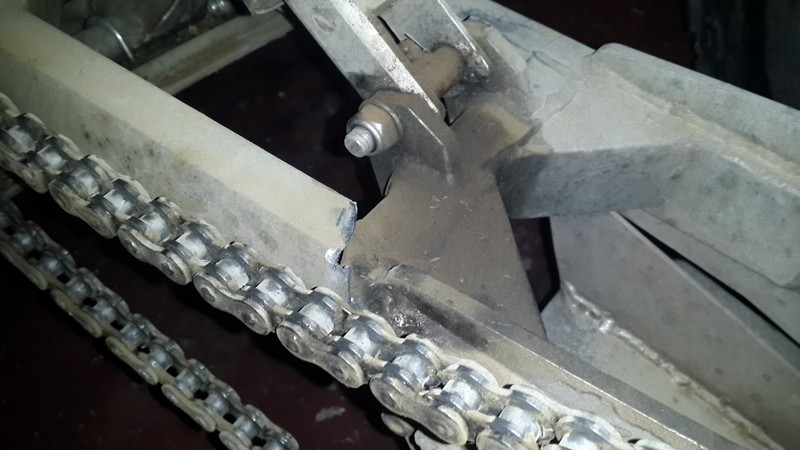
A few years ago, after breaking my standard swingarm, I built my own swinger. Thinking it was rock solid, it too finally gave way...
Turns out the leverage and twisting force applied to the swingarm transmitted through the wheels is pretty enormous! Strong enough to cause metal fatique and shear right through a 50x25x2mm steel.
Its back to the drawing board!
BEFORE:
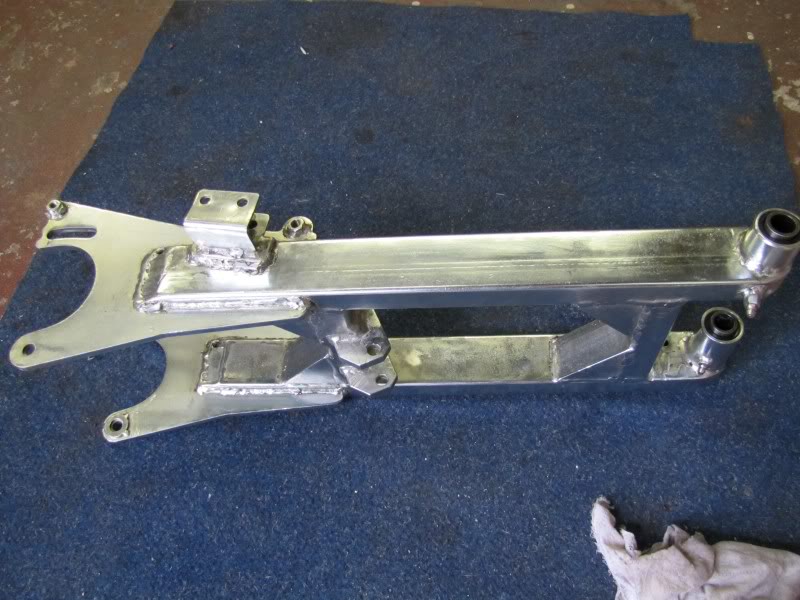
AFTER:
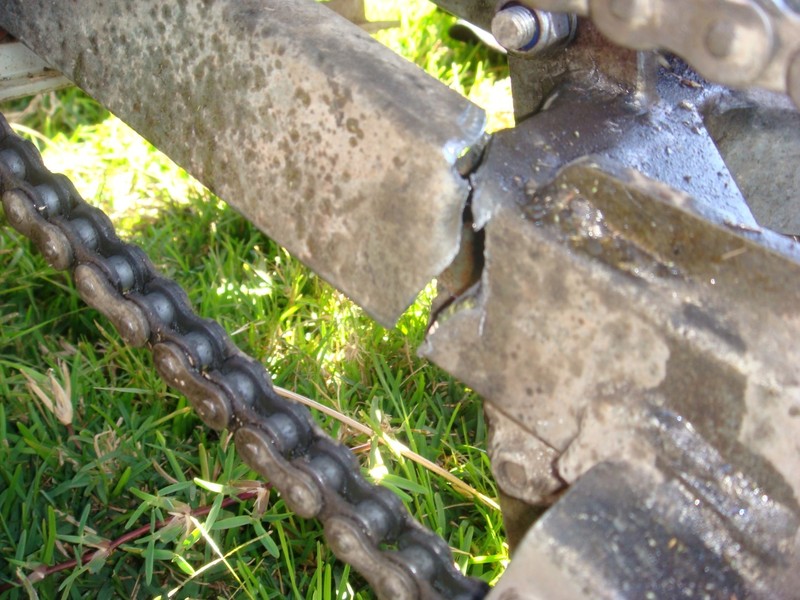
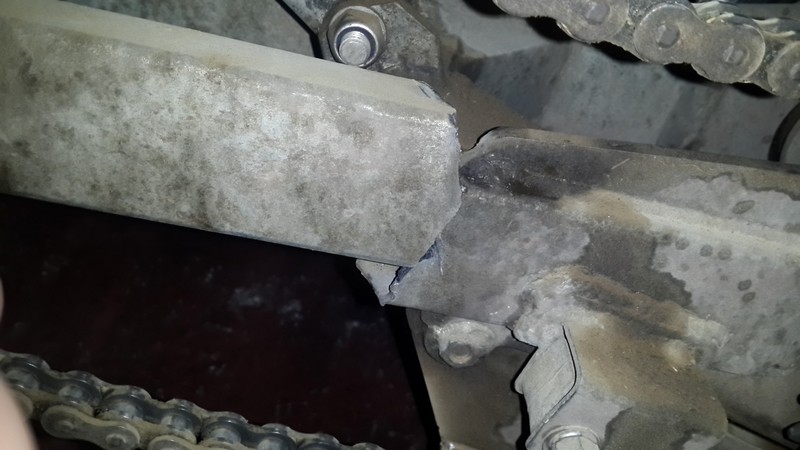
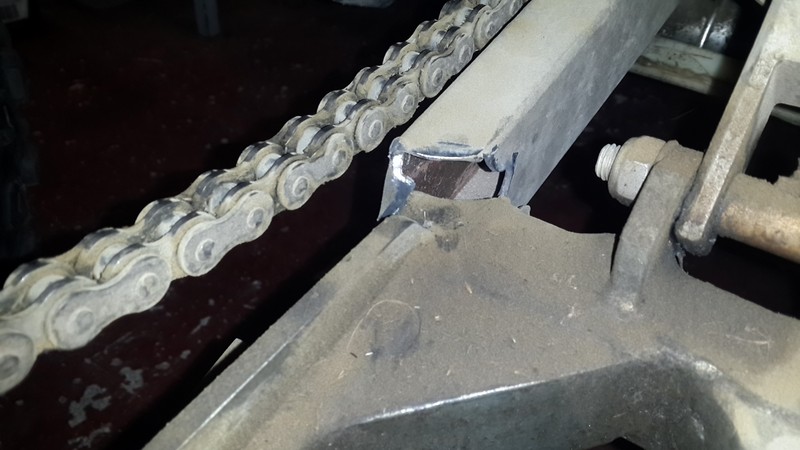
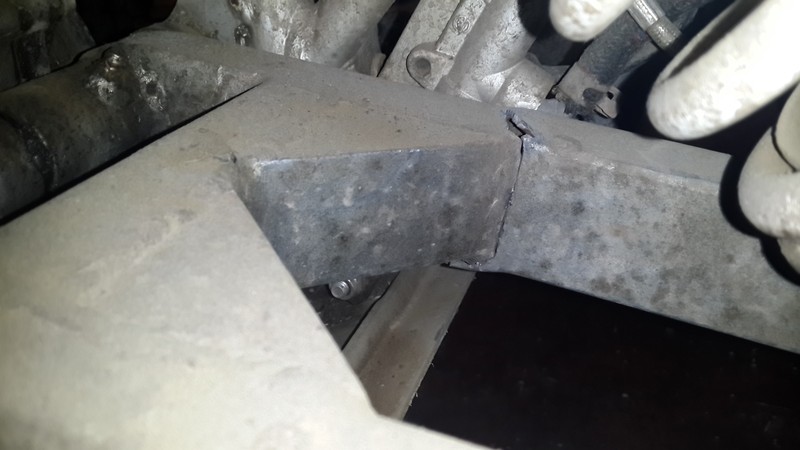
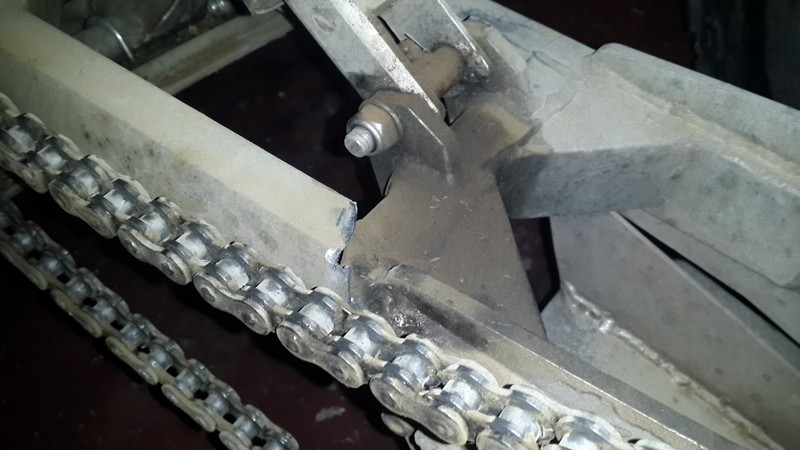
Last edited: